Motivation
Microstructural solidification processes on the microscale have a significant influence on the formation of solidification cracks. Within the framework of the research group project, subproject 6 (SP6) is dedicated to determining the criteria and influencing variables of microstructural solidification cracking, so as to be able to make reliable predictions about the solidification and segregation behaviour as well as the solidification and segregation cracking probability in metallic welds under different process conditions. The research work focuses on the modelling and simulation of the solidification process in a weld, by resolving the microstructural processes and by considering the strongly coupled interactions of chemo-thermomechanical processes. Major challenges in modelling are the process-related high temperature gradient, the multicomponent composition of the microstructure and the thermodynamically consistent mapping of chemomechanical interaction processes.
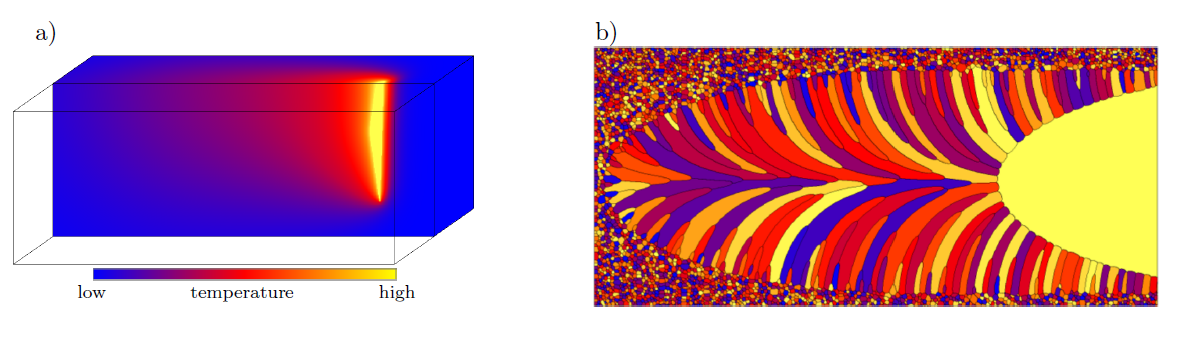
Objective
The objective of the microstructure simulations is to determine the criteria and influencing variables of microstructural solidification cracking, so as to reliably predict the solidification and segregation behavior and the solidification and segregation cracking probability in metallic welds under different processing conditions. In a multiscale mapping, which is superordinate to the research group, information about temperature profiles and concentration distributions in the melt pool is passed from the mesoscale to the microscale and is read in via suitable data interfaces, so as to enable the simulation of solidification. In coupled phasefield chemo-mechanical simulations, the solidification stages of primary dendrites, dendrite blocking, grain boundary formation and complete solidification are calculated and the formation of possible microcracks, resulting from local stress peaks, is predicted. By resolving the microstructural microstructure formation and considering the local temperature distribution, the chemo-mechanical simulations provide the concentration, phase and stress distributions as well as the future microcrack distributions during the solidification and segregation processes. In systematic studies, process-related variables such as the temperature gradient, the welding speed and the heat input are varied and the influence on the susceptibility to crack formation at the dendrite, grain or phase boundaries, as well as in the heat-affected zone and in the melting area, is analysed and forwarded to the mesoscale. From the simulated distribution of microcracks in the solidification structure, statistical parameters of the solidification crack distribution, the solidification crack proportion and the solidification crack formation rate are obtained via data analysis algorithms. Within the multiscale concept, these are transferred to the mesoscale and macroscale as homogenized data. The findings of the simulations on the microscale contribute to the theoretical prediction and classification of metallurgically or mechanically induced solidification cracking.
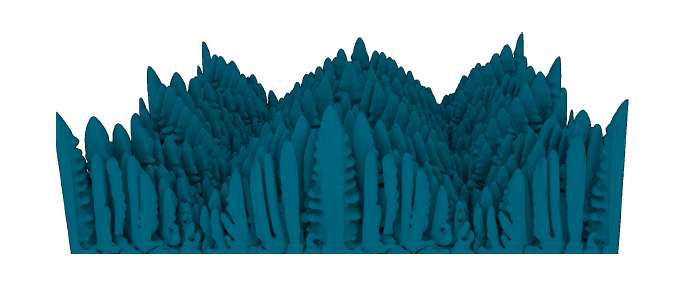
alloy. Source: Institut für Digitale Materialforschung (IDM)
Work plan
To carry out simulation studies on dendritic solidification, the thermodynamic data of the austenitic Fe- Cr-Ni steel, used from the CALPHAD database, are first configured. The formulation of the phase-field model that describes the dendritic solidification of the austenitic Fe-Cr-Ni steel is adapted subsequently, taking into account the chemo-mechanical forces and the strong temperature gradients. After a validation of the newly developed model, simulation studies on dendritic solidification are performed with a ”movingwindow technique”, by varying the process parameters. By applying suitable analysis methods of the threedimensionally resolved dendritic microstructures, the stress and strain distributions are analysed for critical locations and crack formation probabilities are predicted.
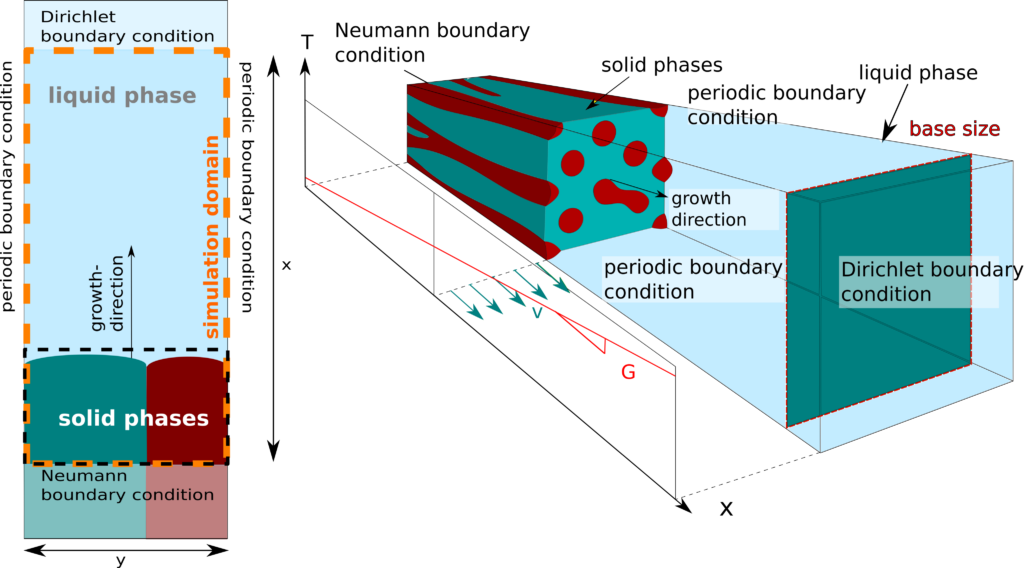
Sub-project management
Prof. Dr. rer. nat. Britta Nestler
Hochschule Karlsruhe – Technik und Wirtschaft (HsKA)
Institute for Digital Materials Research (IDM)
- Email: britta.nestler@kit.edu
Dr.-Ing. Daniel Schneider
Hochschule Karlsruhe – Technik und Wirtschaft (HsKA)
Institute for Digital Materials Research (IDM)
- Email: daniel.schneider@kit.edu
Sub-project researcher
Muhammad Umar, M.Sc.
Hochschule Karlsruhe – Technik und Wirtschaft (HsKA)
Institute for Digital Materials Research (IDM)
- Email: muhammad.umar@h-ka.de