Motivation
By adding alloying elements steels with higher strengths and better formability can be produced. This often results in disadvantages with regard to weldability or the likelihood of crack occurrence. In order to represent and investigate the complex thermomechanical processes in the mushy zone during laser beam welding and the solidification region, which occur on the microscale, and to analyse their effect on the macroscale a multi-scale modelling approach is required. The challenges are the consideration of the multi-physical and multi-scale effects that influence in the process and the mapping of the time-variable microstructure of the solidification zone. For the development of an efficient process simulation software the cooperation of mechanics and mathematics is indispensable. Furthermore information on metallurgical properties on the microscale is needed to develop a meaningful model. The focus is on the development of a highly scalable software implementation of the FE2-method based on the combination of suitable material modelling and solution methods.
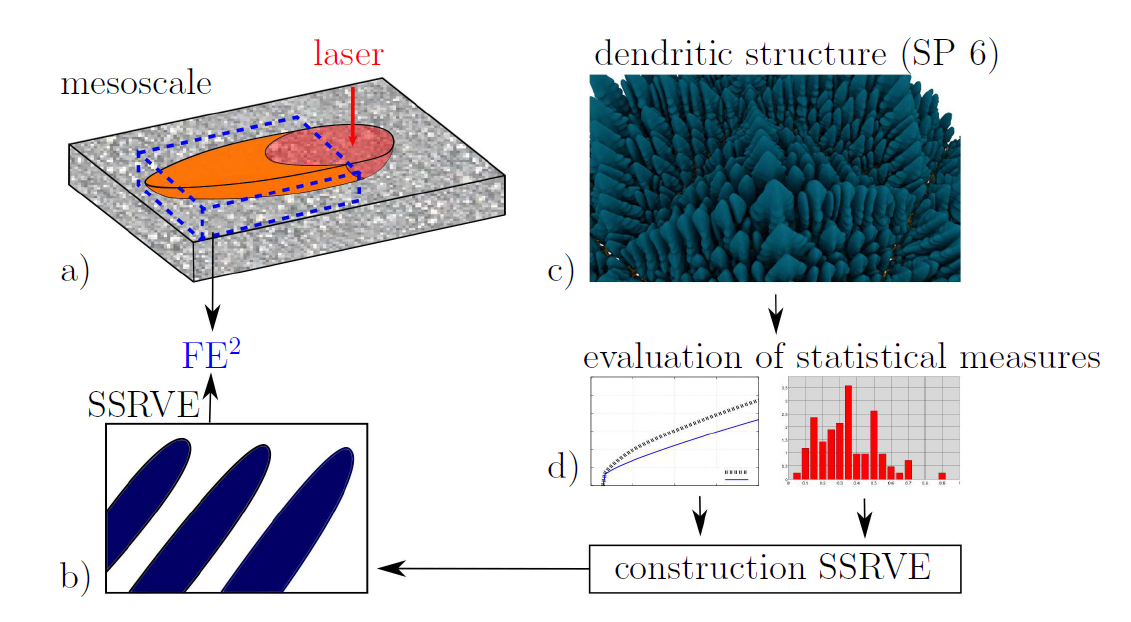
Objective
Within the scope of sub-project 4 (SP4), a multi-scale thermomechanically coupled model for laser beam welding will be developed. The process is considered on the mesoscale, which represents part of the macroscale in the mushy zone, and on the microscale, which refflects the dendritic microstructure in the solidification zone. The two-scale analysis is carried out using the FE2-method. The objective is to determine stress and strain distributions which play a crucial role in solidification crack initiation. In order to efficiently simulate microstructural effects the microstructure will be represented by a statistically similar relevant volume element (SSRVE). Since both, process control and the considered location, produce different microstructure variants, these will be analyzed and evaluated each for their crack sensitivity.
Work plan
For the process simulation of laser beam welding, a heat source model will be implemented in SP4, which will be calibrated with experimental data from sub-project 1 and sub-project 2. In the course of the sub-project, an interface for the integration of the thermofluid-dynamic weld pool model evolved in sub-project 3 will be developed and implemented. The material modelling of the liquid and solid phase fractions of the mushy zone is carried out via a thermodynamically consistent formulation within the framework of thermoelastoplasticity. The developed model will be implemented in the process simulation software environment in close exchange with sub-project 5 (SP5) and used for initial simulation studies at micro and meso levels. To represent the dendritic, variable microstructure in the mushy zone, the approach of SSRVEs will be extended. Data from the literature serve as a basis, which will later be replaced by data from the high-resolution phase field models from sub-project 6. The integration into the software environment for the multiscale simulation of the laser beam welding process will be done in close coordination with SP5. The software developed in this way provides information on stress and strain states in the material as a function of process control and can be used in studies to estimate susceptibility to solidification cracking.
Sub-project management
Jun.-Prof. Dr.-Ing. Lisa Scheunemann
RPTU Kaiserslautern-Landau
Chair of Applied Mechanics (LTM)
- Email: lisa.scheunemann@rptu.de
Prof. Dr.-Ing. Jörg Schröder
Universität Duisburg-Essen (UDE)
Institute of Mechanics (IfM)
- Email: j.schroeder@uni-due.de
Sub-project researcher
Philipp Hartwig, M.Sc.
Universität Duisburg-Essen (UDE)
Institute of Mechanics (IfM)