Motivation
During laser beam welding, the fluid dynamics in the melt pool has significant influence on the quality of the weld and hence the formation of solidification cracks. While experimental investigations are time-consuming and costly, numerical simulations can be a promising alternative to investigate this phenomenon. However, to gain first principle-insights, the simulations must be highly resolved in both space and time. That is, a computational grid consisting of more than 109 elements must be simulated for several hundred thousands of time steps. Such compute intensive simulations are only possible on massively parallel hardware available in modern supercomputers. In order to ensure the simulations’ physical correctness, the implemented models are developed and validated in a close cooperation between computer scientists and production engineers.
Objectives
Sub-project 3 aims to develop and implement mesoscopic numerical models to perform highly resolved fluid dynamics simulations. For this purpose, the physical models are implemented in the software framework waLBerla, which is specifically designed for simulations on parallel high performance compute clusters. The numerical foundation for the fluid dynamics solver is the free surface lattice Boltzmann method (FSLBM), where a Cartesian computational grid is partitioned into different cell types. These cell types are characterized by their fill level. Cells belonging to the liquid phase have a fill level of 1, whereas gas cells are given a fill level of 0. Gas and liquid cells are separated by a single layer of interface cells, each with fill level ∈ (0, 1). The FSLBM inherently assumes that the dynamics of the system is predominantly governed by the liquid phase. That is, the fluid dynamics in the gas phase is neglected, leading to high computational efficiency.
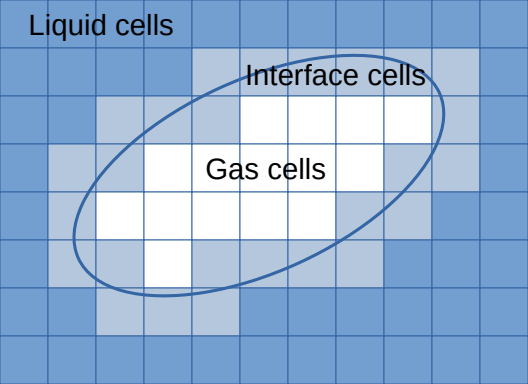
Work Plan
In close collaboration with sub-project 2 (SP2), the FSLBM will be extended by several models, including liquidation, solidification and vaporization. Additionally, a raytracing-algorithm will be implemented to simulate the laser beam’s energy input into the melt pool. During the project, all implemented models will be continuously validated with experimental data from SP2.
The large-scale simulations targeted in this sub-project, can only be realized with a highly efficient implementation of the FSLBM. For this purpose, the FSLBM will be extended with adaptive mesh refinement and load balancing to further optimize the computational performance. Also, to increase the implementation’s maintainability and portability to other hardware architectures, central parts of the FSLBM will be implemented using modern metaprogramming technology.
Sub-project management
Prof. Dr. rer. nat. Ulrich Rüde
Friedrich-Alexander-Universität Erlangen-Nürnberg (FAU)
Chair of Computer Science 10 - System Simulation (LSS)
- Email: ulrich.ruede@fau.de
Prof. Dr.-Ing. Harald Köstler
Friedrich-Alexander-Universität Erlangen-Nürnberg (FAU)
Chair of Computer Science 10 - System Simulation (LSS)
Sub-project researcher
Jonas Plewinski, M.Sc.
Friedrich-Alexander-Universität Erlangen-Nürnberg (FAU)
Chair of Computer Science 10 - System Simulation (LSS)
- Email: jonas.plewinski@fau.de